What is Forging
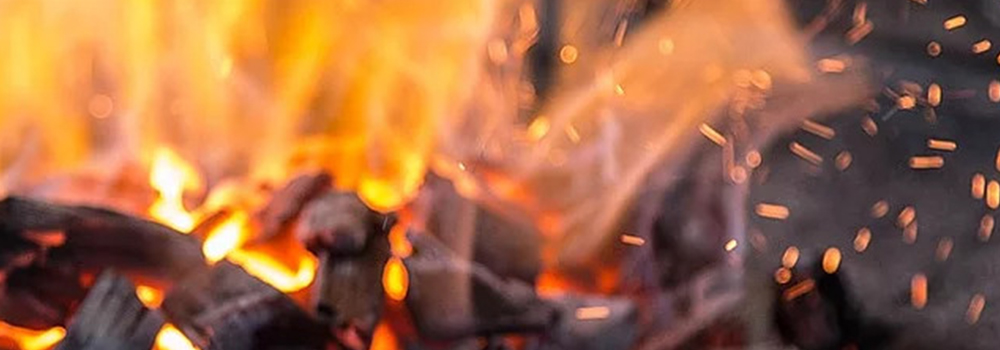
Forging
Forging is a manufacturing process involving the shaping of metal using localized compressive forces. Forging is often classified according to the temperature at which it is performed: cold forging, warm forging, or hot forging. For the latter two, the metal is heated, usually in a forge.
Application
Forging is a very important manufacturing process. Forged part has high physical strength and good tough property. Forging process is used in auto industrial, machine industrial, and construction industrial parts.
Advantages and Disadvantages
Forging can produce a piece that is stronger than an equivalent cast or machined part. As the metal is shaped during the forging process, its internal grain deforms to follow the general shape of the part. As a result, the grain is continuous throughout the part, giving rise to a piece with improved strength characteristics. Additionally, forgings can target a lower total cost when compared to a casting or fabrication. When you consider all the costs that are involved in a product’s lifecycle from procurement to lead time to rework, then factor in the costs of scrap, downtime and further quality issues, the long-term benefits of forgings can outweigh the short-term cost-savings that castings or fabrications might offer.
Some metals may be forged cold, but iron and steel are almost always hot forged. Hot forging prevents the work hardening that would result from cold forging, which would increase the difficulty of performing secondary machining operations on the piece. Also, while work hardening may be desirable in some circumstances, other methods of hardening the piece, such as heat treating, are generally more economical and more controllable. Alloys that are amenable to precipitation hardening, such as most aluminum alloys and titanium, can be hot forged, followed by hardening.
Production forging involves significant capital expenditure for machinery, tooling, facilities and personnel. In the case of hot forging, a high-temperature furnace is required to heat ingots or billets. Owing to the size of the massive forging hammers and presses and the parts they can produce, as well as the dangers inherent in working with hot metal, a special building is frequently required to house the operation. In the case of drop forging operations, provisions must be made to absorb the shock and vibration generated by the hammer. Most forging operations use metal-forming dies, which must be precisely machined and carefully heat-treated to correctly shape the workpiece, as well as to withstand the tremendous forces involved.
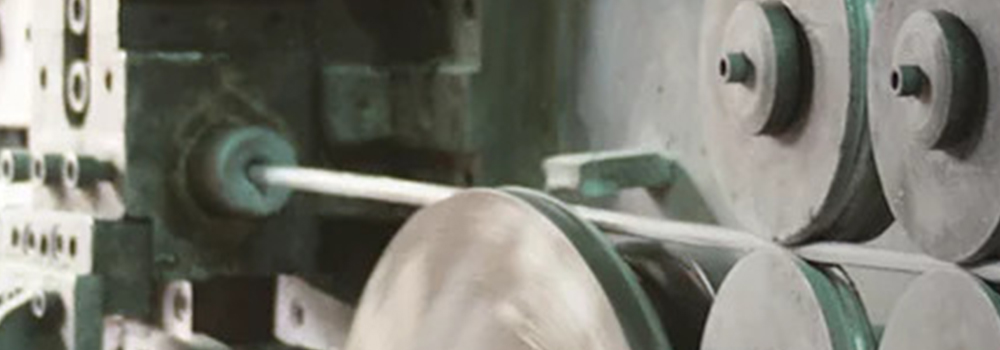
Forging Type
Common forging processes include: roll forging, swaging, cogging, open-die forging, impression-die forging, press forging, automatic hot forging and upsetting
Drop hammer forging machine
Drop forging is a forging process where a hammer is raised and then "dropped" onto the workpiece to deform it according to the shape of the die. There are two types of drop forging: open-die drop forging and closed-die drop forging. As the names imply, the difference is in the shape of the die, with the former not fully enclosing the workpiece, while the latter does.
Advantages
- Reduced chance of voids.
- Better fatigue resistance.
- Greater strength.
- Finer grain size.
- Improved micro structure.
- Continuous grain flow.
Disadvantages
- Not very economical for short runs due to the high cost of die production.
- Drop forging presents a dangerous working environment.
Press forging machine
Press forging works by slowly applying a continuous pressure or force, which differs from the near-instantaneous impact of drop-hammer forging. The amount of time the dies are in contact with the workpiece is measured in seconds (as compared to the milliseconds of drop-hammer forges). The press forging operation can be done either cold or hot.
Advantages
- Higher productivity than drop forging.
- Greater accuracy in terms of tolerances.
- More complicated shapes can be forged.
- Possibility of process automation through mechanism of blank feeding and forging removal.
- The operation is completed in a single squeezing action.
- The press forging, therefore, is suitable for mass production of nuts, bolts, rivets, screws, break levers, bearing races, valves, etc.
Disadvantages
- The initial capital cost is higher compared with drop forging.
- The difficulty of descaling the blank is another short coming of this process.
- The process is economically suitable only when the equipment is efficiently utilized.
Forging Part Manufacturing Considerations
For forging part manufacture, the designer should consider the following: shape, parting line, draft angle, corner radii, fillet, wall thickness, tolerance and machining allowance.

Principles of shape design for forgings
- The forging can have the least finished surface.
- It needs to be suitable for forging technology.
- Make it as simple and symmetrical as possible.
- Avoid sharp section changes, excessive material accumulation, strong direction changes and sharp edges.
- The connecting part should have a sufficient arc angle
- Avoid excessively concave or convex corners, lines or narrow ribs.
- The parts with high dimensional accuracy are concentrated on the upper mold or the lower mold as much as possible.
- Make it as easy as possible to cut off the scrap edges of forgings.
Design of parting line
Parting line is the plane where the two die halves meet along the forging. Usually the first step in designing forgings is to determine the position and shape of the parting line.
- The position of the parting line should be avoided as far as possible in the deep recessed part, because the forging die may be broken in the deep recessed part, or the phenomenon of lack of meat may occur, which makes it difficult to form the part.
- The position of the parting line should be so as to avoid lateral thrust, because the lateral thrust will cause mismatch during forging, which will reduce the service life of the forging die and also affect the accuracy of the forging.
- The parting line should be on the same plane as possible to make the forging operation and mold manufacturing easy.
- The position of the parting line should be considered in accordance with the metal flow situation and economic principles. Sometimes too much attention is paid to the distribution of forging flow lines, which often causes forming difficulties and increases costs.
- It is better to make the metal forging streamline parallel to the forging surface and increase the cost.
- The position of the parting line should use the natural draft angle as much as possible.
- The parting line should make the upper and lower molds symmetrical as much as possible.
- The shape of the parting line should be able to help the cutting edge to remove burrs.
The design of the draft angle
After the parting line of the forging is determined, in order to make the forging easy to take out from the forging die, it must be inclined at an angle in the forging direction around the forging. This angle is the draft angle.
- There is no set rule to set the angle of the inclined die. It usually depends on the forging material, forging shape, forging forming equipment, forging method, etc. The most common draft angle is five degrees.
- From the perspective of material saving and shortening of cutting processing time, the smaller the draft angle, the better, but too small will cause difficulty in demolding, so special attention should be paid when selecting.
Design of inner and outer rounded corners
If there are sharp inner and outer corners in the forging, it will be difficult for the material to flow, and the phenomenon of insufficient material flow to the die cavity will result in the formation of the defect of Cold shut. Too small an external fillet will cause stress concentration in the forging die, and at the same time deform due to thermal fatigue, shortening the life of the forging die. So there should be proper internal and external rounded corners.
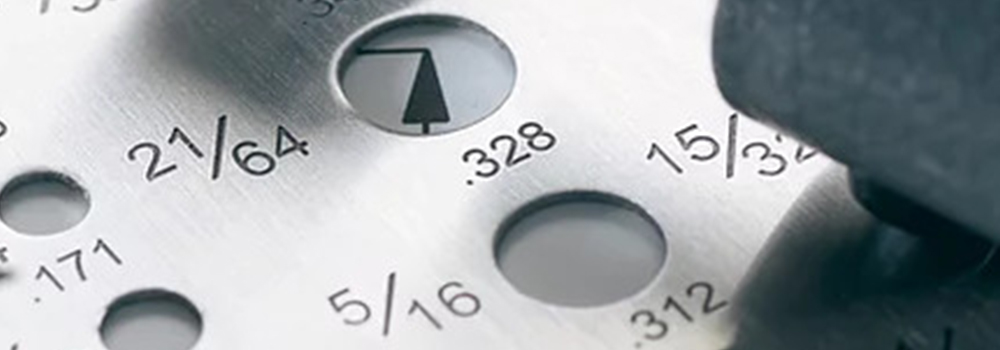
Forging tolerance
The tolerances of forgings are usually determined by the nature and shape of the forgings. The narrower the tolerances, the higher the standard of the forgings. However, the number of manufacturing processes will increase accordingly. Therefore, it is not necessary to set the tolerances too tightly.
Many countries have set standards for forging tolerances. Generally, there are drop hammer and mechanical pressure forging machine hot forging tolerances depending on the forming equipment. Forgings generally have two levels, namely ordinary and precision.
Prerequisites for setting tolerances
- Forging weight: the actual weight of the forging.
- Types of parting lines: there are three types of parting lines: straight, symmetrical and asymmetrical.
- Different forgeability of materials: The forgeability of materials is based on the amount of carbon content or the sum of the quantities of various alloy components.
- Volume ratio of forgings: thin forgings or multi-branched forgings, due to various shrinkage phenomena, require greater deformation force and greater die wear, so simpler and concentrated forgings are better.
Machining margin of forging
Since forgings often need to be machined after forging, the margin required for machining must be reserved in the design of forgings. Before determining the machining margin, it is necessary to understand and analyze the specific size and shape characteristics of the forgings.
The factors that affect the machining margin are:
the shape of the finished forging, the material of the forging, the surface condition of the blank, the processing method used, the processing machine, the processing tool and the number of forgings, and the following benefits:
- Reduce material waste.
- Improve the life of cutting tools.
- Shorten the processing time.
- Reduce costs.