鍛造小知識
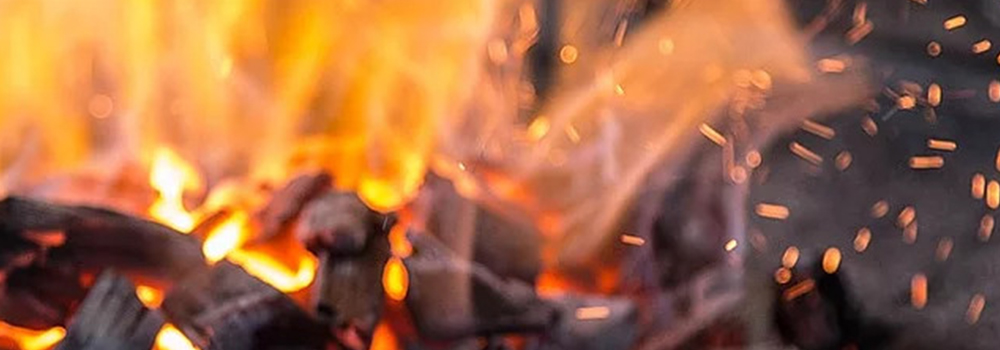
鍛造的意義
鍛造(Forging)是一種使用壓力使金屬成型的加工方法,他是藉著衝擊或擠壓的方式,使金屬材料產生塑性變型,在大部分的製程中,為使材料軟化易於加工,常需將胚料加熱再行鍛打。
鍛造的應用
鍛造是一種相當重要的加工技術,鍛品有物理性能高,韌性好,強度高的特性,可鍛用在車輛上,礦業上,汽車工業上,機械工業上,化學工業上,土木建築工業等等的重要配件。
鍛造的優點
優點
- 相同零件的加工,施以鍛造較其他一般機械加工,其晶粒組織更細密,且減少內部之氣孔等缺陷。
- 可獲致連續的晶粒流動而成機械性的纖維化狀態,材料因而能得到最大分向性的強度,耐衝擊及抗疲勞等優良機械性質。
- 形狀複雜零件,較機械加工更具經濟性,且適合大量生產,降低工件成本。
- 藉著金屬成型流動的方式,鍛造加工比其他切削加工,更可節省材料,減少材料耗損。
缺點
- 高溫鍛造容易氧化,工件表面迅速產生一層銹皮,當鍛造工件與金屬接觸時,銹皮會不斷脫落。
- 由於有氧化物的產生,因此工件精確度無法相當高。
- 鍛造用模具造價高,故不適於做少量生產。
- 鍛造製程變數很多,因此掌握不易,影響製程及結果之況製與成效。
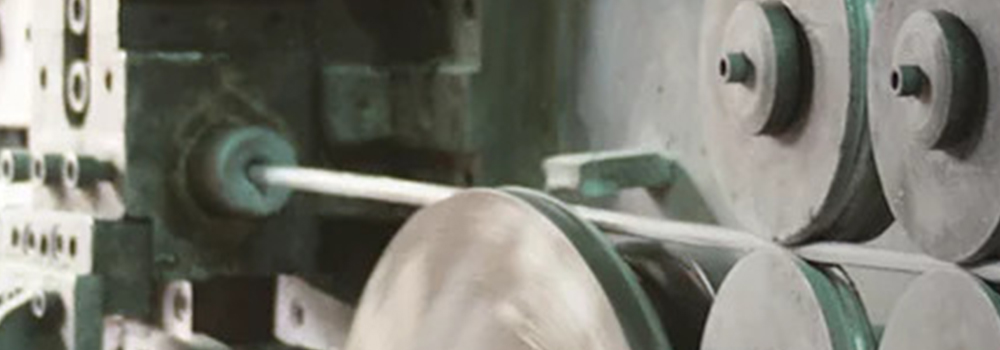
鍛造機的種類
為配合生產力及品質的提高,現今大都採用機械鍛造,而鍛造所使用的機器設備可概分為落錘鍛造機及壓力鍛造機。
落錘鍛造機 (Drop hammer forging machine)
係利用鍛錘(Ram)及上模自某一高度落下產生衝擊力作用於胚料,使材料產生塑性變形以成型的機器。
優點
- 鍛造力量之大小可以自由調整。
- 無上下死點,不會發生過大負荷。
- 每單位時間鍛擊次數多,可逐步增加鍛胚之變形。
- 機器構造簡單,設置成本,生產費及保養費較低。
缺點
- 鍛擊之震動力極大。
- 因震動而會導致模具鬆動及鍛件失正。
- 鍛件品質易受機器操作人員之技能所受影響。
- 生產力較差。
壓力鍛造機 (Press forging machine)
係以一定的壓力,使胚料在鍛模模穴內成型的機器。應用此種機器來鍛造,因胚料受力時間較長,鍛造能量不僅施於胚料表面,且亦傳達到心部,所以表裡受力一致,鍛造品質較佳。
優點
- 比落錘式鍛造機有更高的生產率。
- 衝擊力比同能量的落錘鍛造機更小。
- 比落錘鍛造機需求更少的操作技巧。
缺點
- 如與生產相同的鍛件的落錘鍛造機相比較,則最初的投資價值高,約為期三倍。
- 因壓力鍛造機是以等壓力在連續的衝程施壓,因此在初步形狀鍛造時較不易配合。
- 壓力鍛造機比落錘鍛造機較少能配合不對稱鍛件的鍛造。
鍛件設計的基本概念
(Forging design)對整個成型影響甚大,因此設計人員必須考慮周詳慎重為之。鍛件設計時,通常應考慮的設計要項有鍛件形狀,分模線,拔模斜度,內外圓角,肋及腹板,鍛件公差及加工裕留量等。

鍛件的形狀設計原則
- 使鍛件能有最少之完工加工面。
- 需能適合於鍛造技術。
- 盡可能使其有簡單及對稱的形狀。
- 避免有陡急的斷面變化,過度的材料堆積,強烈的方向的轉變及稜銳之邊緣。
- 連接部分應有充分的圓弧角。
- 避免有過分凹入或凸起的角,線或窄肋。
- 尺寸精度高的部分盡可能集中在上模或下模上。
- 盡可能使鍛件廢邊切除容易。
分模線的設計
分模線(Parting line)或稱分離線,分割線,它是上下鍛模的分開線,通常設計鍛件的第一步驟就是決定分模線的位置與形狀。
- 分模線的位置應盡量避免在有深陷(Deep cavity)部位,因如在深陷部位有可能使鍛模破裂,或產生欠肉現象,使該部位成形困難。
- 分模線的位置應使避免發生側向推力,因側向推力會使鍛造時發生錯模(Mismatch),而降低鍛模的使用壽命,也影響鍛件的精度。
- 分模線應盡可能在同一平面,使鍛造作業及模具製造容易。
- 分模線的位置應依金屬流動情形並配合經濟原則作雙重考慮,因有時太重視鍛流線分佈,則往往引起成形困難,並增加成本。
- 金屬鍛流線以平行於鍛件外形表面較好,並增加成本。
- 分模線的位置應盡量利用自然拔模斜度角。
- 分模線應盡可能使上下模對稱。
- 分模線的形狀應能有助於剪緣去毛邊。
拔模斜度的設計
鍛件分模線決定之後,為使鍛件易於從鍛模取出,還須於鍛件周圍沿鍛造方向傾斜一角度,此角度即為拔模斜度(Draft angle)。
- 斜模斜度大小的設定並無依訂的規則可循,通常需按鍛造材料,鍛件形狀,鍛造成形設備,鍛造方法等之不同而異,最普通的拔模斜度是五度。
- 從材料的節省及縮短切削加工時間來看,拔模斜度是越小越好,但過小將造成脫模困難,故選定時應特別注意。
內外圓角之設計
由於在鍛件中如有銳利的型穴內外隅角,會使材料流動困難,產生流動穴模不足的現象(Flow through)現象,以致形成冷夾層(Cold shut)之缺陷,太小的外圓角(Corner)將使鍛模產生應力集中,同時因熱疲勞而變形,縮短鍛模壽命,有適當的內圓角及外圓角。
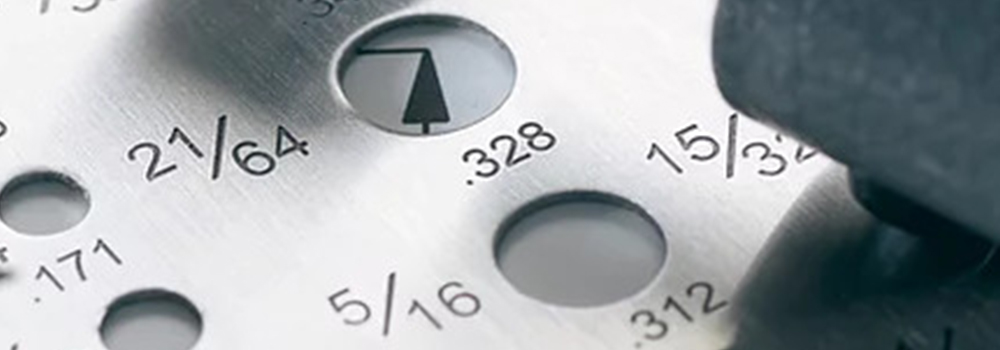
鍛件公差
鍛件之公差通常依鍛件性質,形狀等而定,越狹窄的公差則表示鍛件水準越高,但相對的其製造的工程數也隨之增加,因此,非必要最好不要將公差訂的太嚴。很多國家對於鍛件公差皆訂有標準,一般依成型設備而有落錘與機械式壓力鍛造機熱鍛件公差,而鍛件之品及一般有兩級,即普通即與精密級。
訂定公差的先決事項
- 鍛件重量:鍛件設計圖的真實重量。
- 分模線的類型:分模線有平直,對稱彎曲及不對稱彎曲三種。
- 材料異鍛性:材料易鍛性以含碳量之多寡或各種合金成分數量種和為標準。
- 鍛件容積比:薄鍛件或多叉之鍛件,因各種以收縮現象,形力及較大的工具耗損,故較簡單而擁擠在一起的鍛件之尺寸更不穩定。
鍛件的加工裕度
由於鍛件於鍛造後,經常需要在進行機械加工,故鍛件設計時須預留加工所需的裕度,於決定加工裕度之前需先對鍛件特定尺寸及形狀特性有所認識與研析。
影響機械加工裕量的因素有:
完成鍛造件之形狀,鍛件材料,胚料表面情況,用之加工方法,加工機器,加工工具及鍛件數量等下列益處:
- 降低材料浪費。
- 提高切削刀具壽命。
- 縮短加工時間。
- 降低成本。